CNC enhances manufacturing accuracy by enabling micron-level control, ensuring uniformity across productions, allowing complex designs, reducing human errors, and making real-time adjustments during production
Advanced Positioning and Precision
CNC machines use advanced positioning strategies to provide a high level of manufacturing accuracy. These systems are vital to industries where the slightest error can have significant repercussions.
High-resolution servo motors and feedback systems:
Perhaps the most valuable feature of modern CNC machines, is the high resolution servo motors that gives unprecedented movement control. These motors, when paired with sophisticated feedback systems, allow machining tools to function within extremely tight tolerances, often in the micron realm. In the manufacturing of aerospace components, for example, exact positioning is indispensable for bringing about the aerodynamic properties it demands.
Intelligent software algorithms
Onboard software: The application which operates the CNC’s machines for calculating the most complex part that can help in the positioning of the machining tools. These algorithms can account for variables like tool wear and material variability and, as a result, are highly accurate throughout production. The electronics industry, in which the components are often minuscule, uses these aspects to maintain the integrity of very small and intricate parts.
Automated Tool Calibration:
Many CNC machines come equipped with automatic tool calibration, to detect and adjust variances in tool alignment without human intervention. This is important for the long production runs, where little errors can accumulate along the time. In precision-critical sectors such as medical device manufacturing, where accurate device function is crucial, automated calibration helps to maintain a level of accuracy that doesn’t vary with each new measurement taking operation.
Rigidity and Stability in Design of Moulding Machine:
The physical layout of CNC machines also aids in detailing them to have a high level of precision. Wide-assured material helps to reduce vibration and increase stability, which affects accuracy. When high-strength materials are machined, the rigidity of our CNC machine allows for a constant tool path, even under the influence of machining stress.
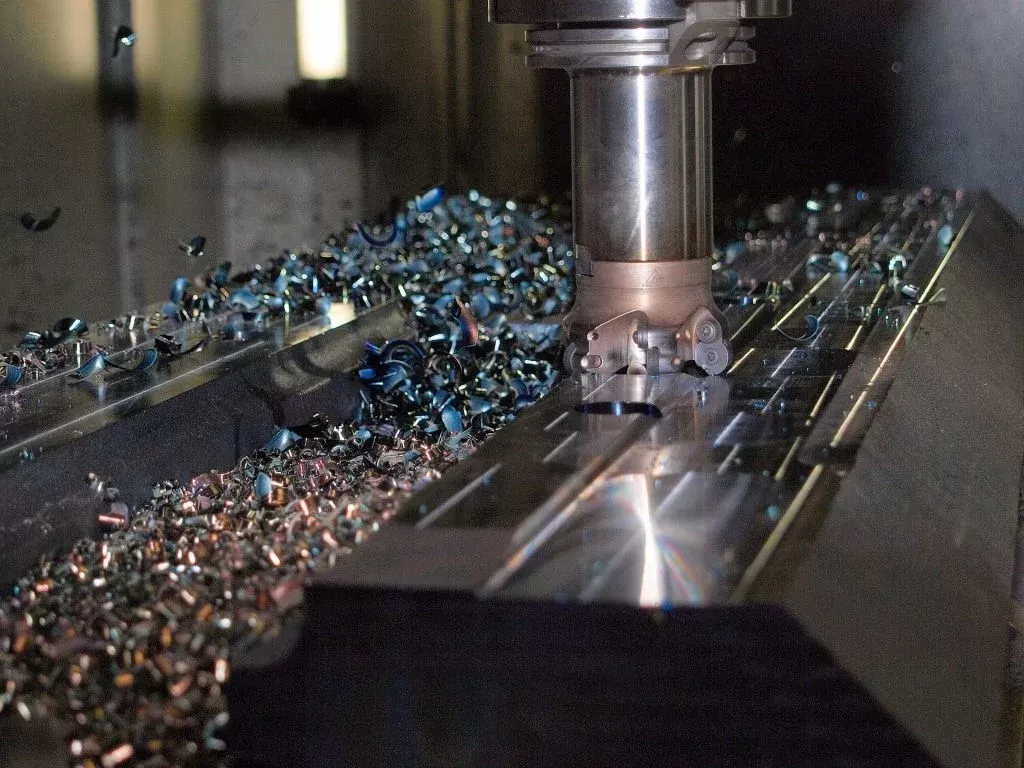
Consistency in Production Batches
a high-volume manufacturing environment, where having consistency between production batches is an absolute must, CNC machining is vital. Accomplished through orchestrating and replicating exact machine movements and settings from part to part.
Exact Digital Templates and Settings
CNC machines work off of digital blueprint files that define the exact parameters and path for each operation. In the automotive industry an example would be the requirement of producing engine parts according to a very precise set of specifications in order to fit properly with other components explained above. These parts are capable of being made to 0.0005 inch tolerance thanks to CNC.
Fully automated tool changes and calibration.
CNC Machines increase the consistency of the batch with the help of automatic tool changes and calibration. The plan, for the moment at least, is to teach them how to work with Computer Numerical Control (known as CNC) machines so that they can program and set up an automated machine to run multiple parts with different tooling and settings within a single operation, all with no human interference and minimal chance for an error to occur. In the consumer electronics sector where components like PCBs (Printed Circuit Boards) are precision crafted, a CNC machine can ensure that, the entire production fits exactly the same across thousands of units.
Real-Time Monitoring and Quality Checks
Most newer CNC systems use real-time impedance sensing that monitor the process, and adjust as necessary. If there are any abnormalities in the tool wear or discrepancies in material, sensors will measure and then control the machine accordingly to adjust the status-quo. In sectors like aerospace and defense, where the smallest of irregularities can result in considerable operational challenges this system comes in handy.
Uniform Material & Easy To Handle:
This assists CNC machines not simply to oversees the authentic cutting and forming procedure yet also to promise that the course of action of taking care of and stacking the materials too is consistent. This decreases the variability due to material placement and orientation; hence increasing the batch consistency.
Complex Shapes and Detailed Designs
CNC milling are known for their top performance ability to handle complex shapes and designs without errors as manual processes do. This ability is critical to sectors such as the aerospace, automotive, and fine arts industries for which precision and detail are key.
Advanced CAD/CAM Software
More complex geometries are manufactured using CNC that needs Computer-aided design (CAD) and computer-aided manufacturing (CAM) software. With these programs, designers can make complex 3D models, which CNC machines can translate and implement. For example, in the aerospace industry, CAD/CAM software is used to create intricate inside areas of engine pieces required when weight saving and fuel consumption are key factors.
Multi-axis Machining:
This is because of the usually 5-axis nowadays and sometimes 7-axis capabilities of 21st century CNC machines that allow for the tool to move across control multiple axes at once! It has 2-axis movement and is capable of machining very complex shapes without re-clamping the workpiece. One example is in the manufacture of orthopedic implants, where a 5-axis CNC machine can produce the complex, sculpted shapes and intricate details needed to mimic the human body.
High Precision Tooling:
High-precision tools can produce small features that are fine or like the thickness of a hair on humans, and that is only possible with CNC machines. Precision details such as this are crucial in industries like electronics, where an error of even a few micrometres can throw the design of the finest of smartphones or tablets. With daily sharpening and restoration of those instruments, Machines are kept like new condition decades after their GC purchase.
Material Versatility:
A CNC can work on many types of materials, soft plastics all the way up to titanium, all with very high accuracy on different material properties. Such diversity is essential for tailor-made manufacturing contracts, for example, detailed moulds for new consumer products that need to incorporate both metallic and plastic parts.
Highly Developed Finish Techniques
Post-machining: After the machining, a CNC machine can also do detailed finishing operations such as polishing or engraving to either add capabilities to a part or simply aesthetically please it. For instance, CNC machines are used to produce minute embellishments in luxury watches and they are always identical from one piece to another.
Reduce Human Error and Rework
This is important for the sake of efficiency and cost-savings in manufacturing, as CNC machining is all about less human error or minimal need for rework.
Automated Precision:
Work that was once done by a human operator has been automated using the programing parameters instituted for that task to be performed on CNC machines. This move to automation reduces the risks that come with manual measurements and tool handling. Speaking of which, in the automotive industry, calculating everything down to the millimeter is how software in a CNC machine ensures that engine parts are manufactured with precision– because even being off by 0.001 is enough to make an engine go kaboom, literally. Automated processes are fine tuned to this design and manufacture each part exactly how the CAD model specified, so no or little rework is needed.
Streamlined Production Process
CNC machines are less variable, for instance, than a manual machining operation where the skills of the machinist and the quality of machining in the last lot done are different each time. Standard designs guarantee that each part is almost identical, and help to eliminate part-to-part variability which equates to fewer defects. The consistency that CNC machines provide enables them to create error-free, high precision chips while decreasing the likelihood of lower-quality failures in fields such as semiconductor manufacturing where the micrometer level of precision is necessary on a daily basis.
IT Systems
CNC machines have quality control systems integrated, and are capable of performing real-time checks during manufacturing. The systems can detect anomalies when they are happening, enabling the process to make feedback corrections immediately before parts make a production run of bad parts. This is crucial for the maintenance of best practice and for the compliance with health and safety protocols in cases such as among precision engineering applications for medical implants.
Training and Simulation:
More advanced CNC systems have simulation programs in place which allow the computer to be told what to do but can be done in a sort of virtual machining process away from the actual machining. This helps to eliminate some of the errors in programming and setup, contributing significantly to rework and scrap in traditional manufacturing setups. As an example, aerospace manufacturers use simulations to guarantee that complicated parts meet exacting design requirements before cutting into expensive materials like titanium.
Loops and Adaptability :
CNC machines are also modernized, with the latest models even having adaptive feedback systems to modify the machining parameters using sensor data. The system is able to correct for tool wear or temperature changes, and thus reject those suspected problematic shots. This ensures that in application areas like precision tool manufacturing, where tolerances are absolutely crucial, the final workpieces always remain within the defined limits of measurement and the need for rework is minimised drastically.
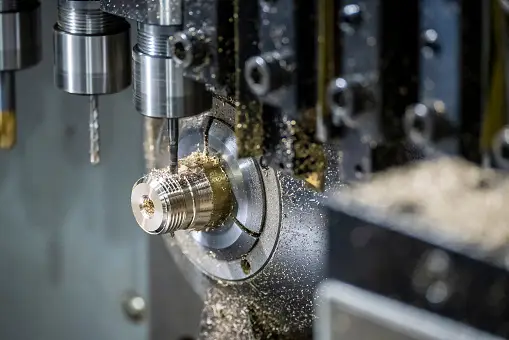
Speed and Efficiency for Precision Tasks
As the leading example, CNC machining is capable to produce parts with high precision in a very efficient manner, providing elasticity to considerably speed up the cycle times and effectiveness of the production process, especially when it comes to complex and precise works.
Rapid Material Removal Rates:
The modern CNC machines operate at high-scalespeed and can move the cutting tools very effortlessly with good precision, allowing us to quickly and effectively remove the material. Many times, a CNC milling machine will perform material removal at rate a few times higher than traditional machining configurations. In the manufacture of car parts for example, such speeds can generate parts to the required standard of quality, typically 0.0005 inch diametrical tolerance, very quickly, such as pistons or cylinders.
Optimized Tool Paths:
CNC software can also determine the fastest and most efficient path for a tool to take in order to cut a part with the least amount of time and wear on the tool. This makes the production not only faster but can also extend the life of the tools used for machining. Efficient tool paths in industries such as mold making for plastic products ensures that molds are manufactured quickly and to the tolerances necessary to meet the stringent quality standards required.
Automatic Tool Change and Settings:
Their advanced machining ability to switch tools and quick setups between operations allows for milliseconds time lost (or less), and provides one of the lowest potential downtimes for any CNC machine. The automation enables a smooth, quick handoff between different stages of machining—a significant benefit in high-volume manufacturing environments such as consumer electronics, where multiple, precise operations are needed on a single piece.
Strategies for High-Speed Machining
For these features, fast-moving tools can be used with gentle cutting forces, making high-speed machining a very attractive option. The methods cut out the chance of harming the tool and the material and it also accelerates the process. High-speed machining is used by aerospace manufacturers to create intricate components, such as airframe structures, that require both precision and performance.
Lean Manufacturing Integration:
CNC machining is typically integrated with lean manufacturing systems to improve overall workflow efficiency. This integration is via lean manufacturing principles as well as waste minimization through efficient CNC operations with a just-in-time production approach. Lean principles paired with CNC precision machining make it possible to quickly produce implants and surgical instruments in the medical device sector, having little inventory, and with a high quality at the same time in-line with the demand.